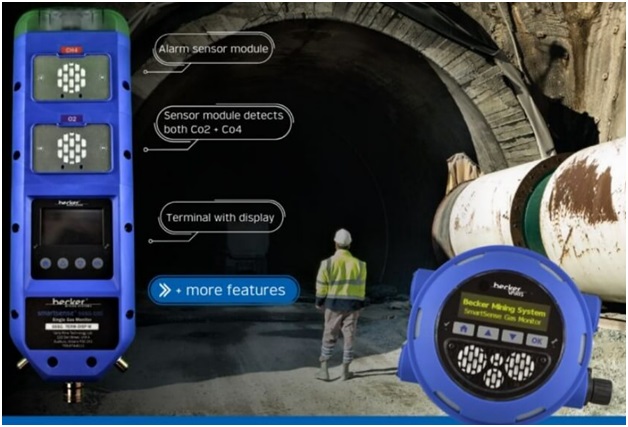
Gas detectors typically undergo calibration and bump testing to verify they function correctly and accurately detect gas presence. Here is a brief overview of each type of testing:
- Calibration: Calibration exposes a gas detector to an accurately known concentration of the gas it intends to detect and then calibrates it to read the correct level. Calibration usually involves using an accredited calibration mixture traceable to an established standard.
- Bump Testing: Bump testing involves exposing the gas detector to a controlled amount of gas to verify that its alarm functions and sensors are functioning correctly. Miners should conduct this type of test before each use of the gas detector to guarantee its efficiency.
- Functional Testing: Functional testing involves verifying all other features of a gas detector are functioning correctly, such as visual and audible alarms, battery life, and other features.
- Periodic Testing: Gas detectors may require routine testing at specific intervals to guarantee they remain working correctly and accurately detecting gas levels. The frequency of regular testing will depend on the type of detector and application.
Following the manufacturer’s recommendations for testing and maintaining gas detectors is essential to guarantee they function correctly and provide accurate readings. Proper testing and upkeep can help protect workers by avoiding accidents related to gas exposure.
This post was written by Justin Tidd, Director at Becker Mining Communications! For over 15 years, Becker Communications has been the industry’s leader in Gas Monitoring Devices and electrical mining communication systems. As they expanded into surface mining, railroads, and tunneling they added wireless communication systems, handheld radios, tagging, and tracking systems, as well as gas monitoring.